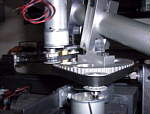 | Here is a tight shot of the pan-tilt mechanism that positions the pneumatic pike on the rear of the Ag. The top motor drives a custom leadscrew actuator to raise and lower the pike. It has a range of horizontal to -18 degrees. The lower motor pans the whole assembly through 270 degrees effectively covering the sides as well as the back. I used a really hard alloy of aluminum to machine the joints since I was using steel pins as axles. The motors were driven by another Tekin Rebel speed controller that in turn was driven by a synthesized signal from the microcontroller, a Scott Edwards Counterfeit Basic Stamp. The Stamp even ran acceleration curves on the motors, similiar to an accelerating mouse cursor. |
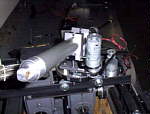 | A shot down the length of the pike. In the final presentation of the Ag I chopped off the clevis mount on the cylinder end to permit better clearance. When the pike is charged it presents a push force of about 150 lbs. The whole mechanism is strong enough to hold this force in the case where the tip dead stops against a target. You can even pick up the whole robot by the pivot mechanism (heck, this applies to most elements on the Ag.) |
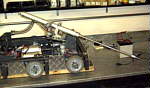 | Showing the pike fully extended. It doesn't hit the ground when lowered to it's fullest extent, but it does come close. |
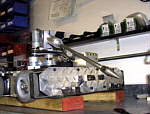 | Position of the pike looking rearward at the Ag. I've also started to enclose the open spaces with aluminum diamond plate. The finished vehicle looks really great (in the August status report.) And yes, those are custom high-tech 2x4 blocks the Ag is sitting on. |
 | It took me forever to figure out how to make the pike move up and down (the "tilt" direction.) I ended up with a small leadscrew actuator built into the pan ring gear, backed up by bearings. The trick was making something strong enough that wouldn't break when subjected to the 150 lb. reaction force of a shot. The other trick was to make it out of aluminum for weight (and because I hate machining steel - see below.) It worked really well. |
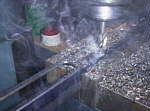 | This is how I machine steel: lots of cutting fluid. Here I am cutting rounded rectangles into one of the gas engine track supports to lighten it. When I was done, I had dropped the weight by 12 oz. which is quite a bit. My wife gets a little scared when she walks into the garage and sees smoke rising from the mill. Especially when I'm nowhere to be found. |
 | The pike from the side. You can also see the titanium wheel guards in place (horizontal) at the bottom of this shot. Teammate Mike made them to replace the steel ones I had machined up in order to increase our sturdiness and decrease weight. Too bad the round stock he used made them weigh just as much as the steel ones. We ended up taking one or both of these off during the competition to stay under weight as we added custom weapons to make our opponents feel special. That empty mount to the right is where the 2-stroke engine attaches. |
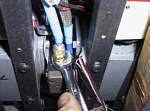 | Toward the end I was really out of space inside the Ag. You're looking at me tightening the air line fittings to the air solenioids which are mounted vertically between the two worm gear speed reducers. I had to work from the bottom because there was too much in the way on top. The plastic lines I used worked great: flexible, cheap, cut to fit and they came in pretty colors. |
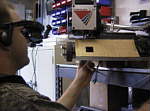 | My neighbor Dean wearing the VIO goggles as we mock up the front aluminum ramp in cardboard. I had no idea what the field of view of the CCD camera was, so I had him wear the goggles and I cut a rectangular hole in the cardboard, widening it as per his instructions. I decided at the last minute to mount the cam in the nose, especially since there wasn't any protected area left on the top deck of the Ag. The camera got it's own custom nylon brace that I shock mounted with neoprene washers to isolate it from gas engine vibrations. |
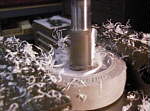 | As I wrote in an earlier status report, the Ag used Colson caster wheels. They come with free-running hubs (like most casters.) The hubs had to be machined off to provide a flat clamping surface for the axles and rim mounts I welded up. Machining plasic is just plain fun. |